45度と30度
積層をする際に、ねじり対策として45度を使用します。
さて、ここで30度を使用したらどうなるでしょうか。
横弾性率
まず、横弾性率から見ていきます。
プリプレグを回転させていった際の目安です。
縦軸を45度の状態を1.0とした維持率、横軸を角度としてグラフにします。
角度による横弾性率の変化 ▼
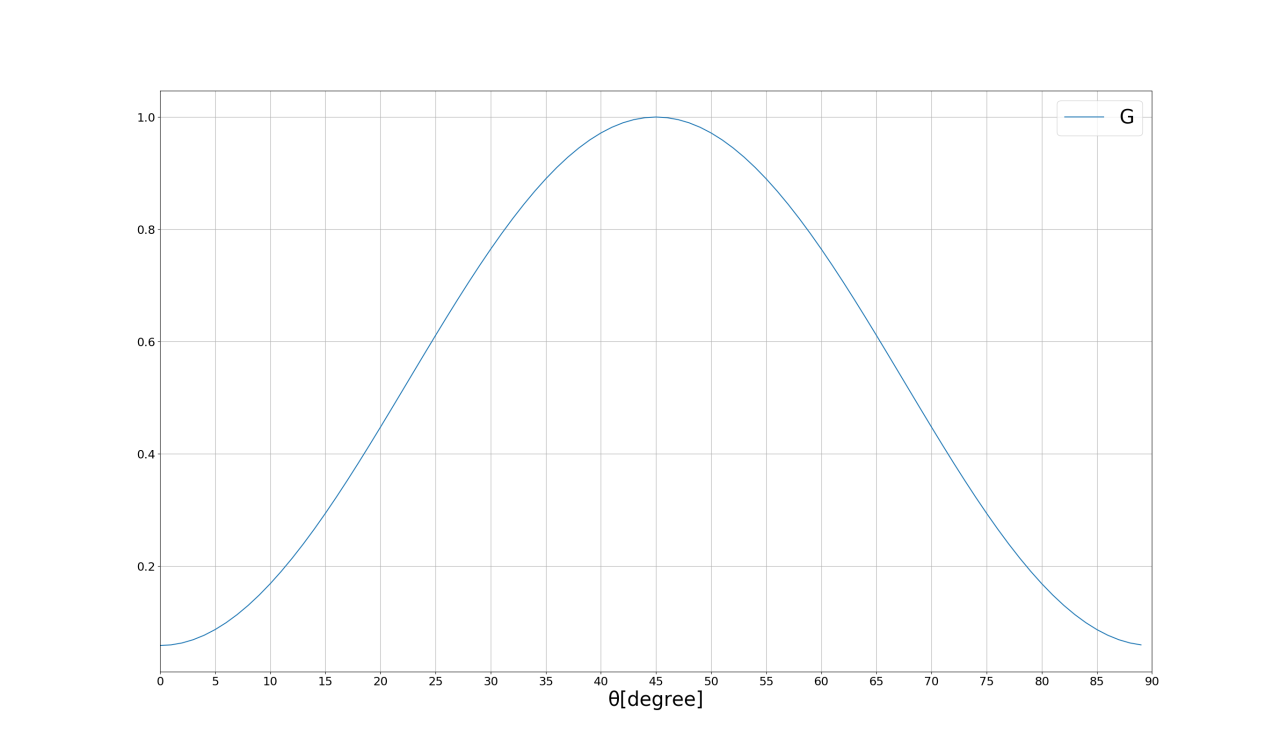
45度を山頂とする山です。
45度を用いる理由が良く分かります。
ここで30度と45度の維持率の差はどのくらいあるのかを考えていきます。
差▼
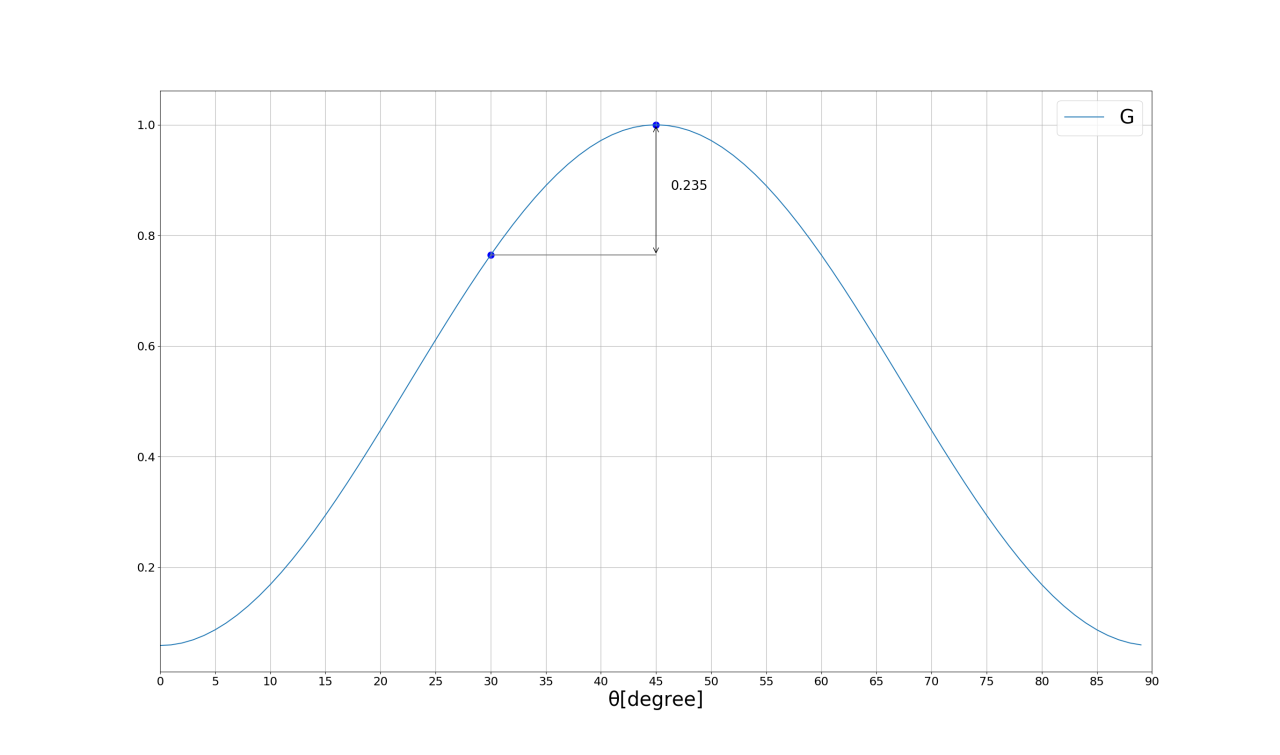
45度を30度にした場合、横弾性率は約24%減少することになります。
縦弾性率
縦軸を0度の状態を1.0とした維持率、横軸を角度としてグラフにします。
角度による縦弾性率の変化▼
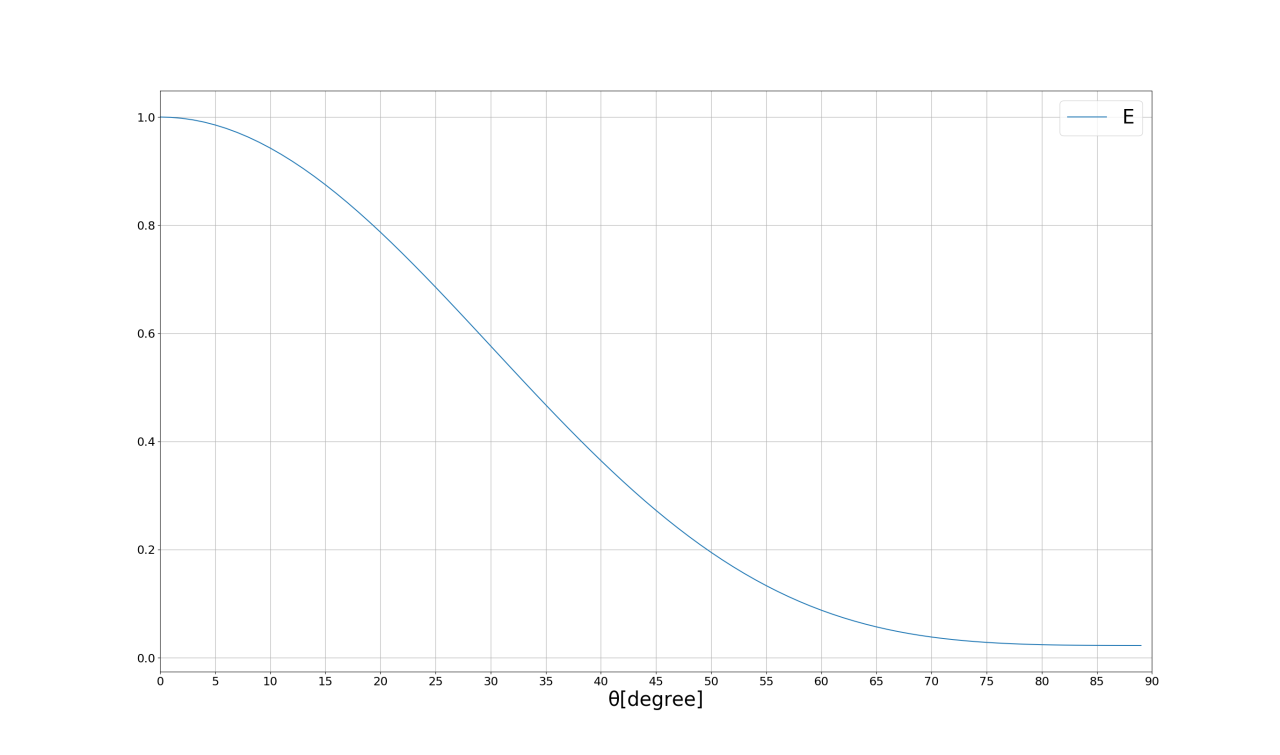
当然のことながら、プリプレグは繊維方向には強い(?)ですが、直交方向は樹脂に依存するため弱いです。
角度を90度に近づけるほど維持率は小さくなっていきます。
45度と30度の差を調べます。
差▼
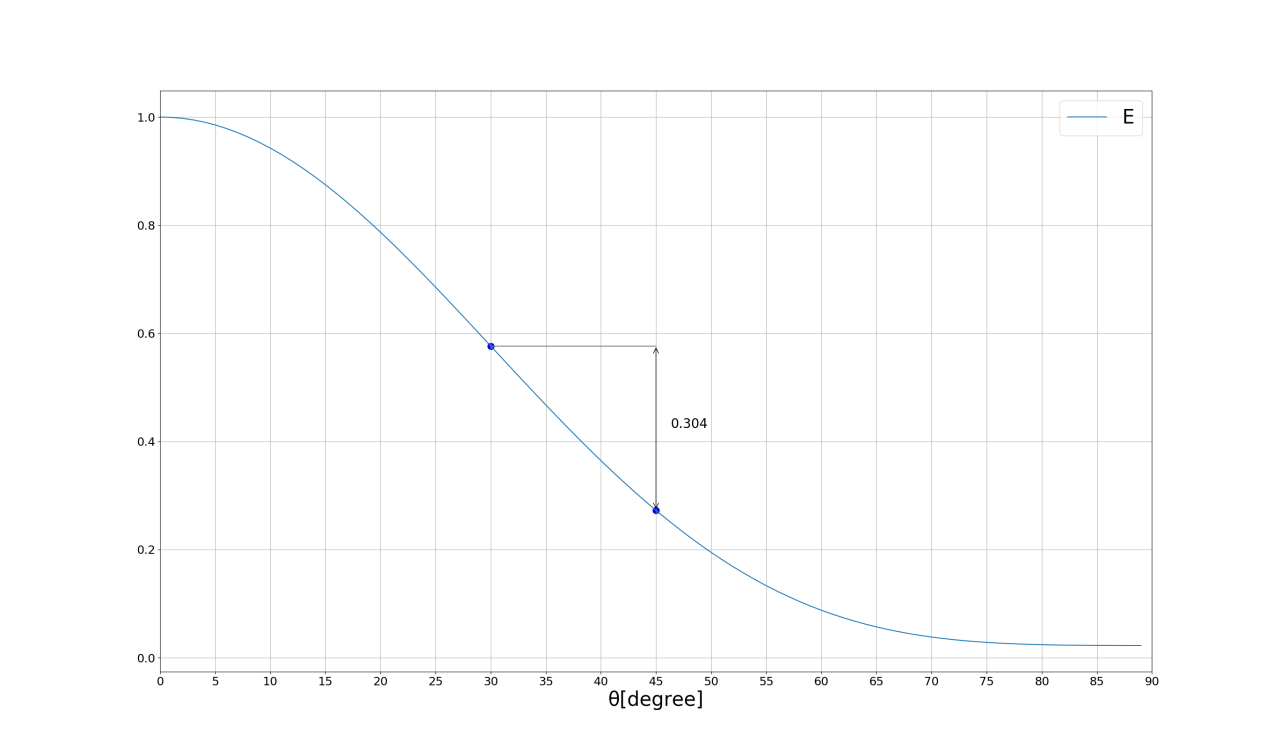
45度を30度にした場合、横弾性率は約30%増加することになります。
まとめ
45度を30度にした場合
縦弾性率 約30%増加 ⤴
横弾性率 約24%減少 ⤵
試しに[0/30/90/90/-30/0]sと[0/45/90
/90/-45/0]sで単板を作ってみました。
(炭素繊維:M40J)の12層積層板▼

0度の縦弾性率が約260[GPa]で、45度の横弾性率が約51[GPa]なので結果への影響もこんな感じですね。
ただでさえギリギリの主桁では採用が難しいかもしれませんが、
尾翼桁、フレーム桁やドライブシャフト等で
採用出来るかもしれないですね。
おわり
下ワイヤーマウント
ワイヤーマウントがあるチームの方が珍しいですよね。
可動式飛行張線接合部って名前らしいです。
(以下キンポでお願いします。)
ワイヤーって邪魔ですよね。
片持ち翼いいなーっていつも思いながら見てます。
最終キングポスト▼
昨年度(17年度)問題点として、
重心位置調整の際にマウントを動かすのに、
ワイヤーマウントは動かさないという
混沌ケイオス状態になってしまうことがありました。
(高さという概念が無かったのは忘れましょう)
じゃぁキンポ動かせる様にすれば良いじゃんってなったのですが、
下フレームと言えば、イス、操縦桿、フレーム接合部など、邪魔な存在が多い事で定評があります。
操縦桿の軸とキンポ一緒にすれば良いということで僕が作りました。
まぁ結局キンポさんは後ろへ行ってしまったので、
別々になりました。
可動式ということでまずフレーム桁とドッキングするパーツを作ることにしました。
変な形のパーツなんて作ったこと無かったのでまずは試しに作ってみました。
初期実験▼
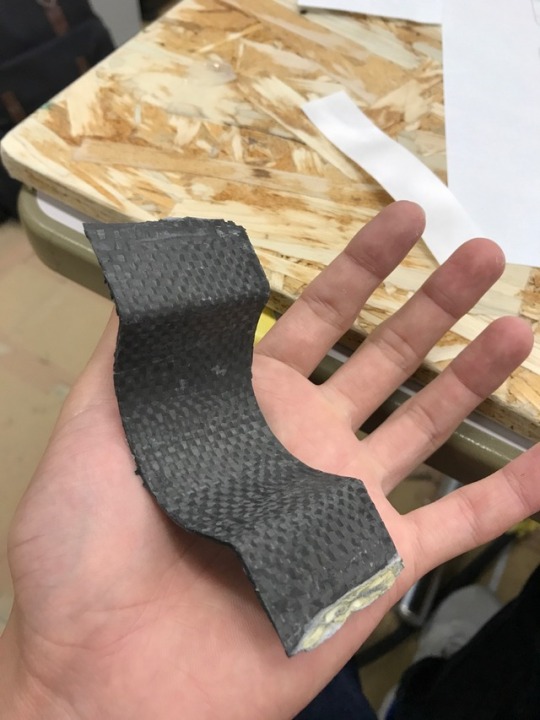
なんかそれっぽいのができそうでした。
この時はホワイトスタイロ+マイクロバルーン+アルミテープです。
真空引きなう▼
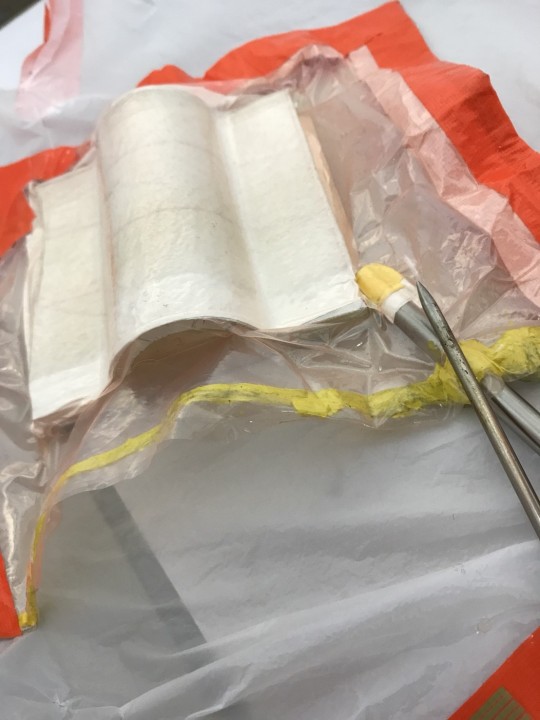
型は一回しか使えませんでした。悲しいです。
型を今度はMDFで製作しました。
MDF型▼
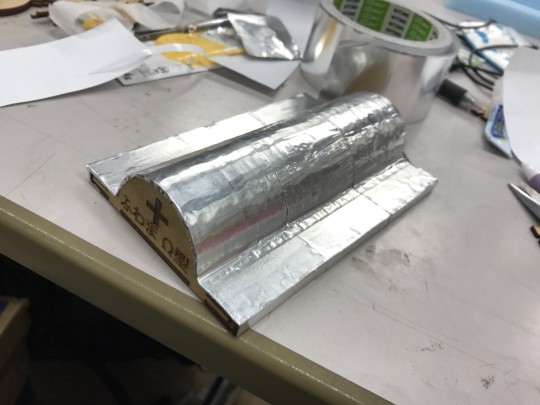
すこしレーザーの精度のせいでぼこぼこしてしまいました。
こんな感じでプライ後に抜く▼
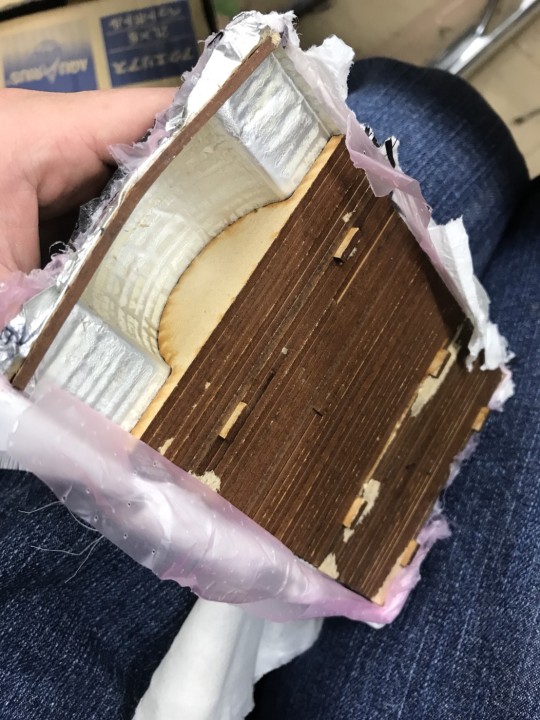
とりあえず再利用はできますが、
正味発砲スチロール+アルミテープでよかった感があります。
とりあえず切ってみた▼
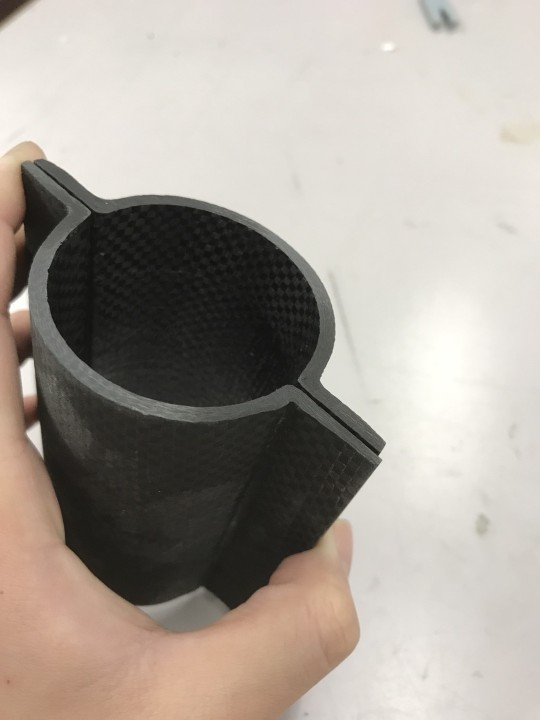
まぁまぁですが、内側が少しぼこぼこしてしまったので、少しやすりました。
極力やすりたくないのですが仕方ないです。
ボルト4点固定用の加工を施します。(穴あけ+固定部サンドイッチ)
斜めから見た固定後▼
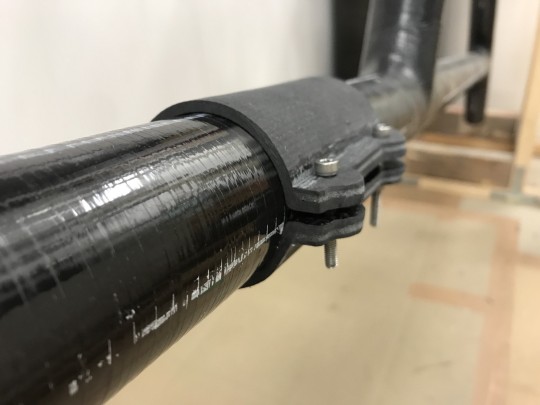
穴は一応スリーブ挿入してみました。
スリーブ挿入後▼

可動部はこんな感じです。
次は棒です。
一応回転は許容していますが、パイプが折れちゃいけません。
(この時はまだ積層理論等詳しくなかったです。)
複合則的に考えて製作した結果、とっても太いです。
60度の層が少し多い故ですね。回転の力はそんなにかからないことに気づいたのが遅すぎです。
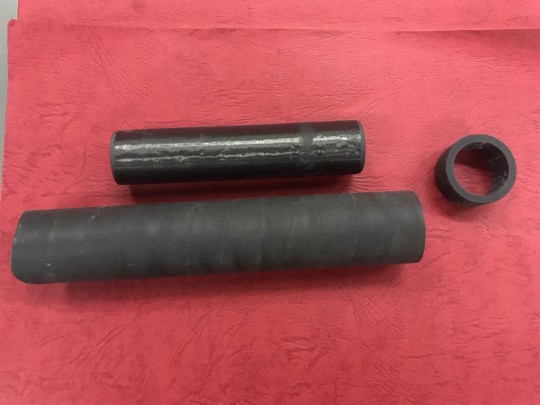
はめあわせのためのやすりは緊張しました。
これをスッと組み合わせます。
組み合わせた後▼
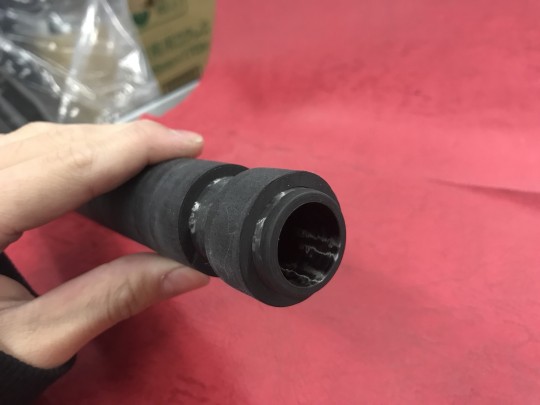
かなり気持ちいはめ合わせでした。幸せです。
可動部と棒を接続するために接着面積を増やしました。
マイクロバルーンで増やした▼
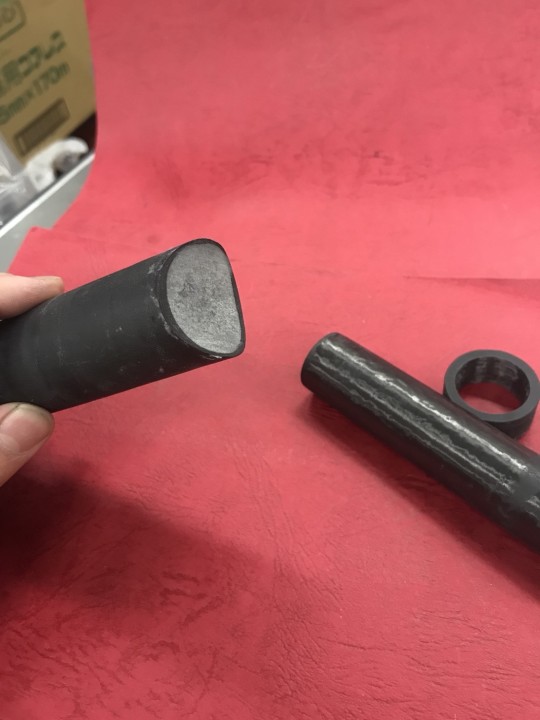
あとはワイヤーを直接つける接合部です。
黄色特化型信号機▼
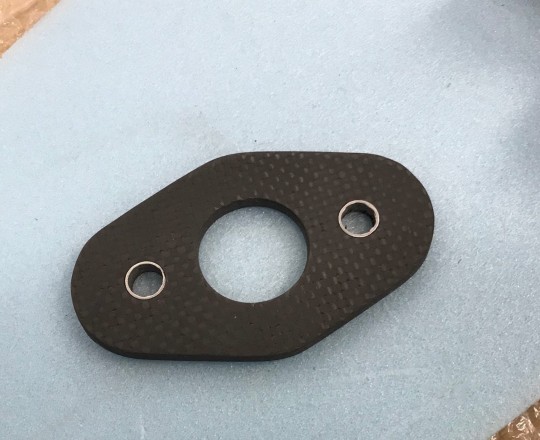
サンドイッチにすればよかったのですが、そこにちょうど厚い板があったので作っちゃいました。
組み合わせるとこんな感じです
組み合わせ▼
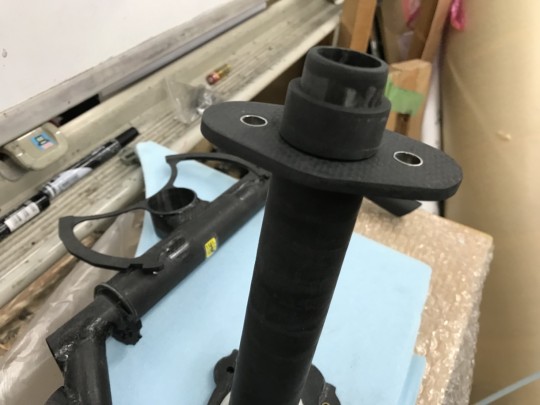
当初はここに操舵桿をつけるつもりだったので、パーツは取り外して桿の取り外しができるようなシステムでした。
しかし、彼は桁試験用になってしまったわけです。
全てをプライすることになりました。
プライ後▼
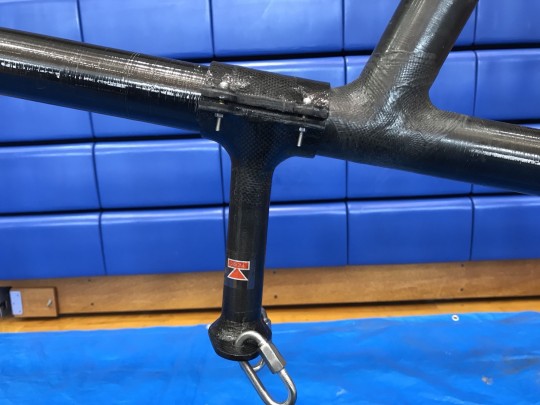
かわいくはないですね。
桁試験前日、とてつもなくしんどかったのを覚えています。
ずっとずっと作ってました。
上の写真からわかるようにちょっと後ろに行くと接合部ですね。
そうです。かなしいです。
作り直します。
接合部に対応していくために、固定は最終重心位置決定後にして、それまではホースバンド固定でいきました。
新たなパーツたち▼
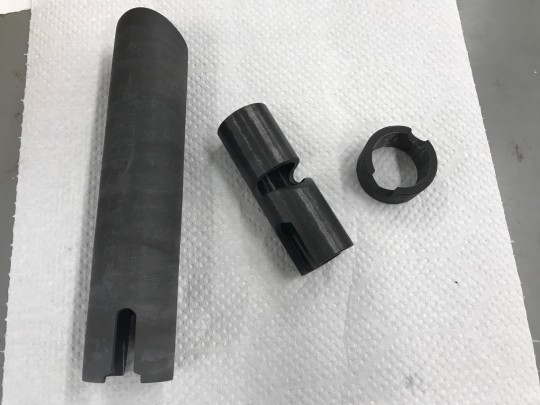
これ+半円のカーボンパイプとなり、かなりシンプルになりました。
ワイヤーはシーリングに付けます。
シーリングを埋め込む感じにしてみました。
ワイヤー接合部▼
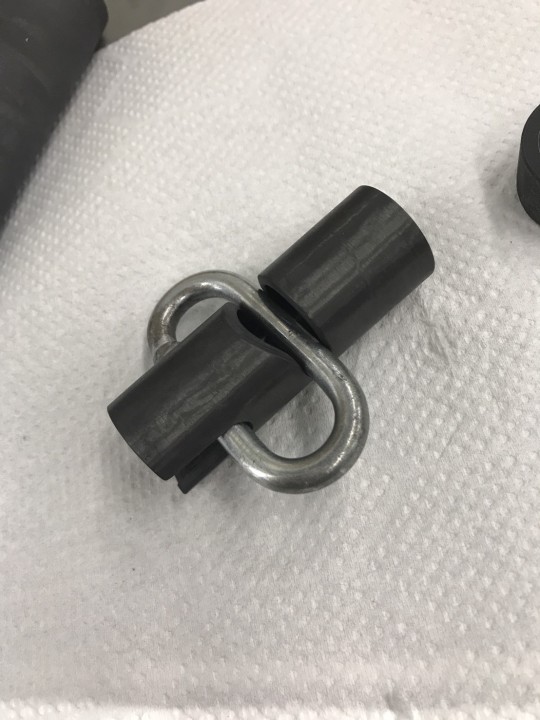
これをすぽっとはめます。
取り外しできるので操舵桿も取り外し可能です。
(つけるとは言ってないです。)
組み立った感じ▼
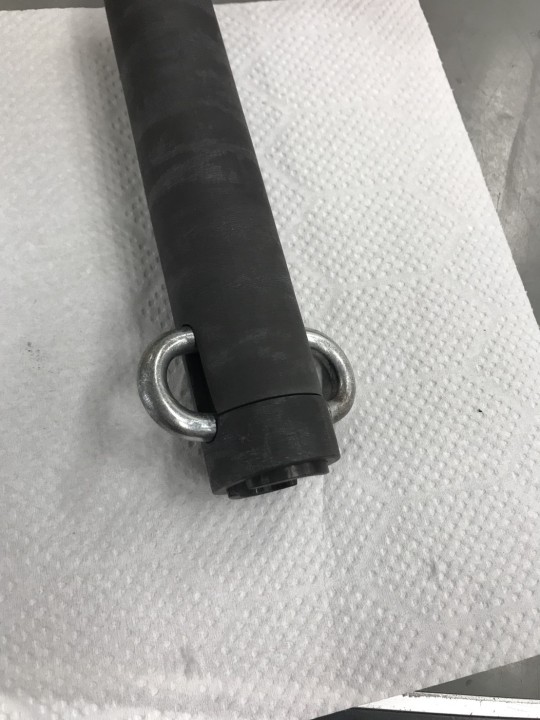
思ったよりきれいにできました。
並べてみるとこんな感じ▼
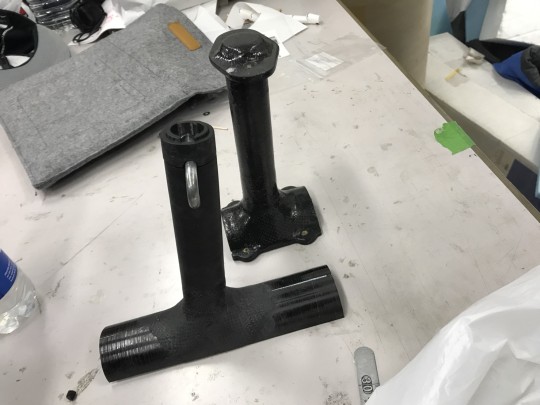
newはシンプルですね。
フレームに付けるとこんな感じ▼
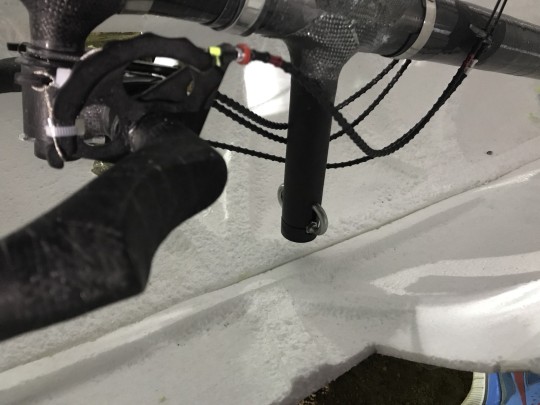
最終的にはパイプはカットしてプライしてしまいました。
反省は何といっても重すぎです。こりゃだめです。
実用的じゃないかもしれないです。
パイプの積層や接合方法を変えてもう少し軽くしないといけないですね。
来年への課題です。
おわり
小径パイプ焼きたい
カーボンパイプ(小径)のまとめです。
パイプはφ23くらいが一番小さかったです。
もっと小さいのも巻けないことは無いですが、めんどくさいです。
まず、マンドレルを製作します。
どこかでアルミの丸棒を買います。
それを旋盤で加工します。
その後、水研ぎやすりでやすります。
小さいマンドレル▼
少し(多少は耐え)段差があると、抜けなくなります。
耐えてるの▼
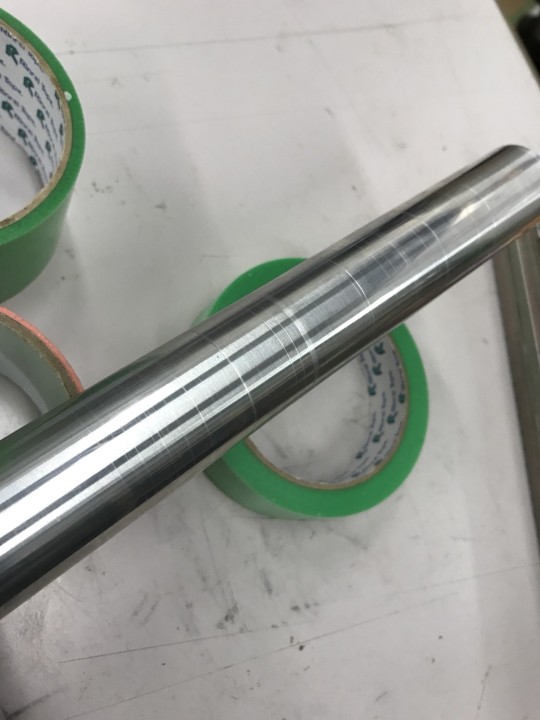
抜けなくなった時▼
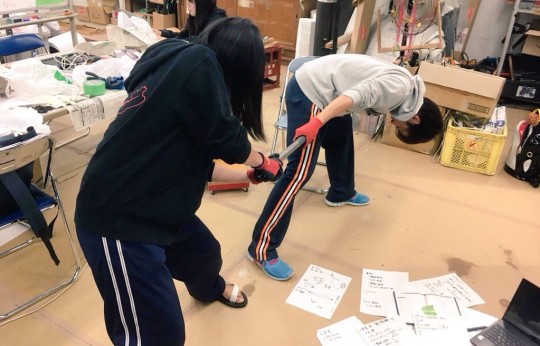
この時は、段差のとこで表面のカーボンだけ切って救出しました。
わんちゃんわんちゃん(0%)といいながら
氷水に浸けていたのはいい思い出です(?)
冷えたパイプ▼
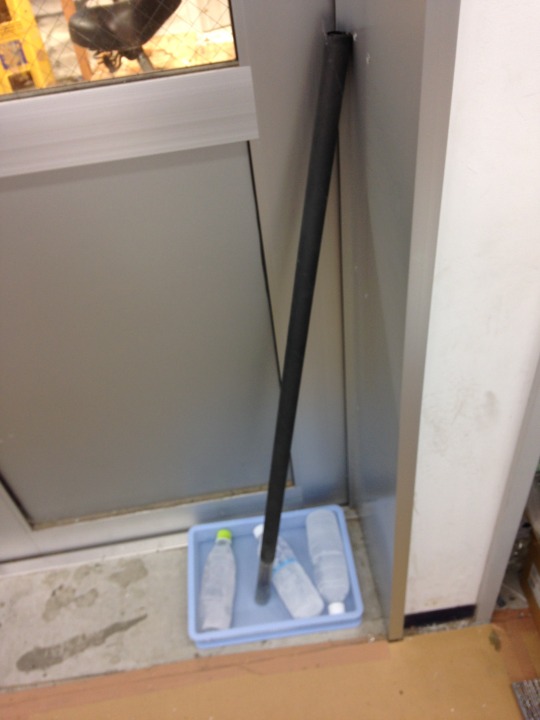
正味、初めてで失敗多数+徹夜で正常な脳みその人は一人もいませんでした。
やはり、徹夜は良くないですね。
やっとこさ作り方
1.離型剤を塗る。
ケムリースと呼ばれる離型剤を使っています。
ケムトレンドジャパン
2.プリプレグを巻く
大切なのは最内層の90度です。
ここさえ超えれば山は下りです。
急がば回れ精神で、ゆっくり着実に曲げていきます。
最内層▼
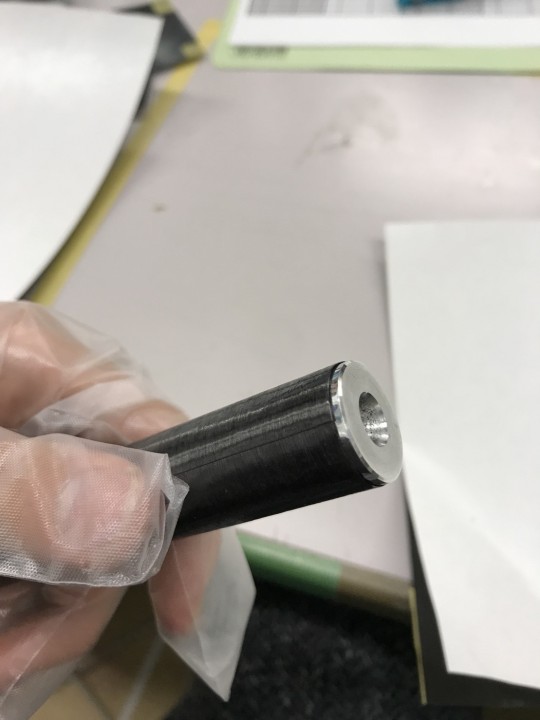
重ね幅は2㎜です。
1㎜とかでもよいのですが、もし足りなかったら悲しいので、ここは諦めます。
途中▼
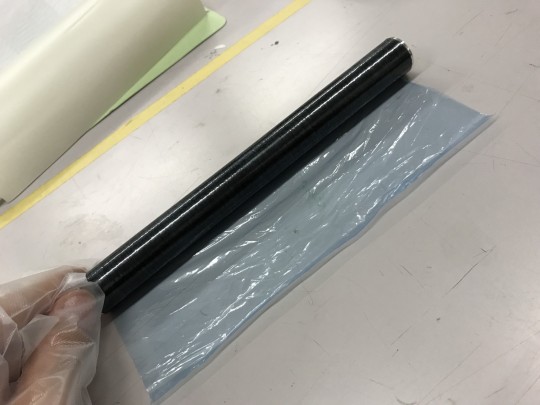
押し付けるようにくるくるっと巻く感じにすると綺麗に巻けます。
雑談
最内層の90度は形状維持といわれていますね。
柔らかいものを選ばないと死にます。
冷却時にピキピキ聞こえたらそれは、
繊維が折れた音だそうです。(某会社情報)
45度なんかも極力柔らかい方が良きです。
45度を太いパイプに巻いた後▼
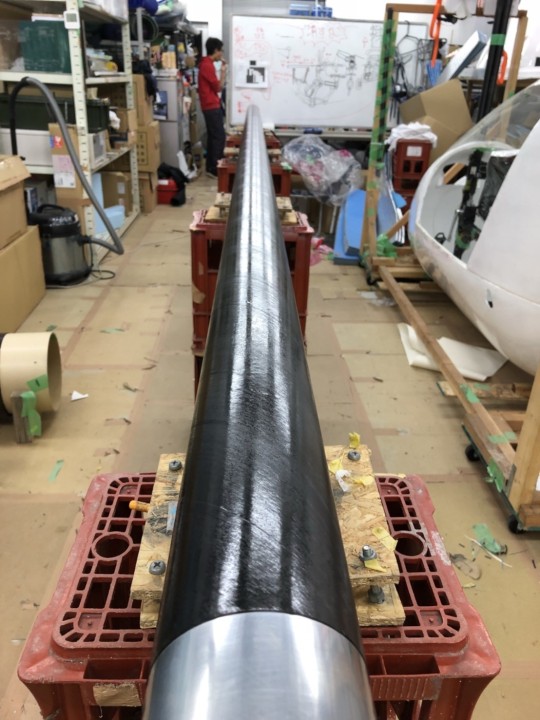
加熱時のひずみは、繊維方向は炭素繊維に依存(?)します。
直交方向は樹脂(マトリックス)です。
マンドレルが長いと90度を巻くときプリプレグ足りないです。
本来90度同士は重ね幅0でも大丈夫です。
その方が段差無くて良いのです。
が、不安だということで結構重ねてますよね。
3.ピールを巻きます。
帯状のピールクロスを巻いていきます。
ハサミで切ればきれいに切れるのに、横着して引きちぎった汚い帯▼
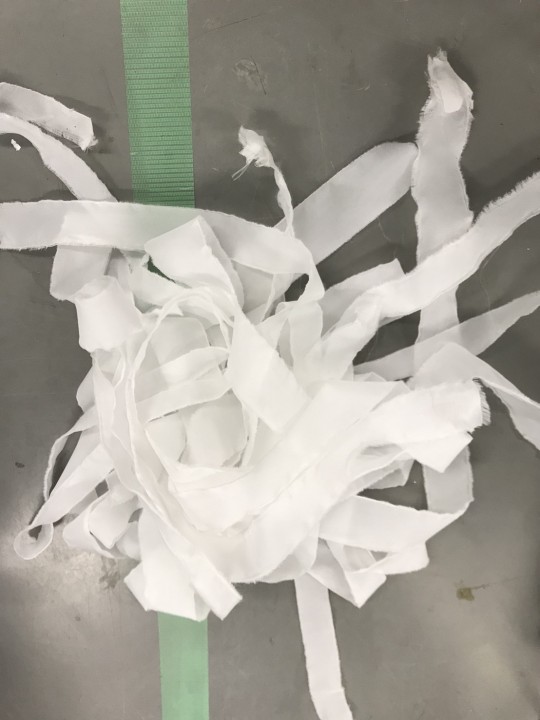
左右のぴらぴらしたとこは無いようにして巻きます。
4.シュリンク巻き
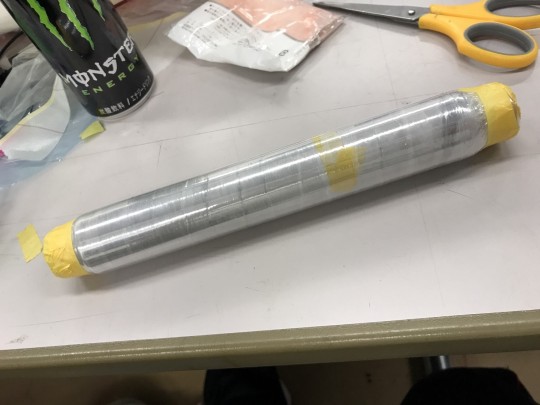
ウインナーに見えます。
5.焼く
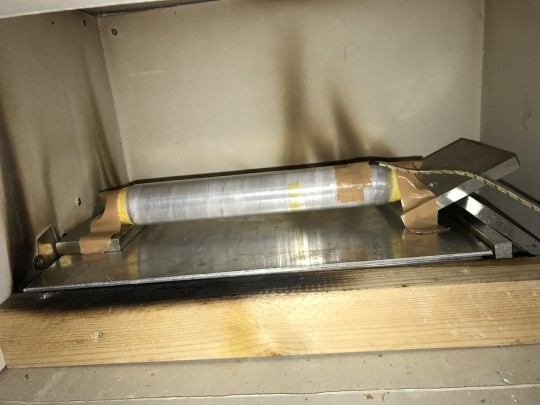
もっとウインナーに見えます。
今まで巻いたパイプで薄いのだと4層でした。厚いので20層強です。
厚いの▼
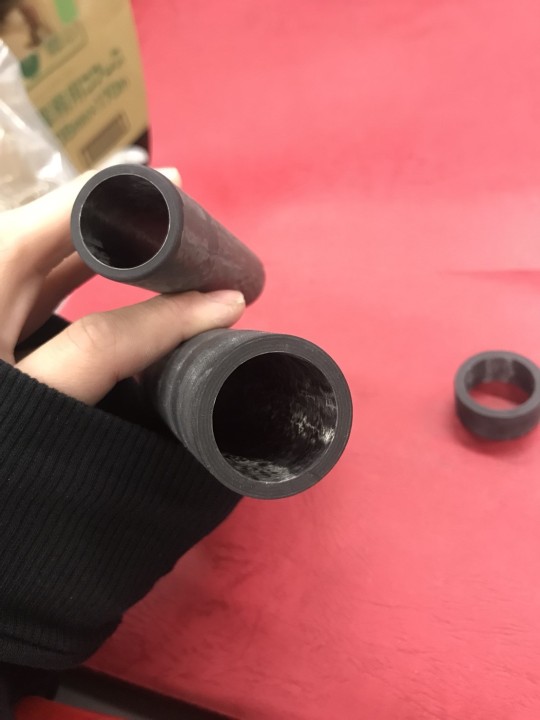
楽しかったです。
おわり
単板焼きたい
カーボン単板の作成工程のまとめです。
基本、製作に使用したCFRPパイプや単板は、プリプレグの状態から積層し、製作したものでした。
単板
1.プリプレグを切ります。(炭素繊維:M40J)
この時のプリプレグカットは嫌いです。
最初はマスキングテープと指金を使って、カッターでカットしていましたが、非常にめんどくさかったです。
途中から、200x300のアルミ板を型にしてカットをすることにしました。
革命でした。
プリプレグカットがやや嫌いになりました。
2.積層します。
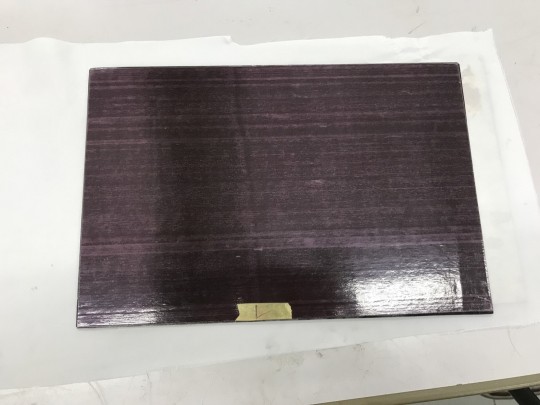
基本積層は[0/45/90/90/-45/0]です。(12層だと対称積層にできます。)
大事なのは積層する角度が急激に大きくならないことです。
層間剝離が起こりやすくなります。
3.マイクログラスを貼る(?)
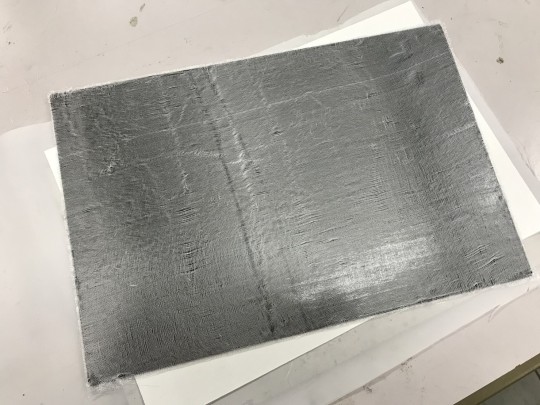
マイクログラスは表面の剥離の防止です。
穴開け加工時に、一生懸命気をつけても、
マイクログラスがないと剥離する時はいとも簡単です。
剥離したの▼
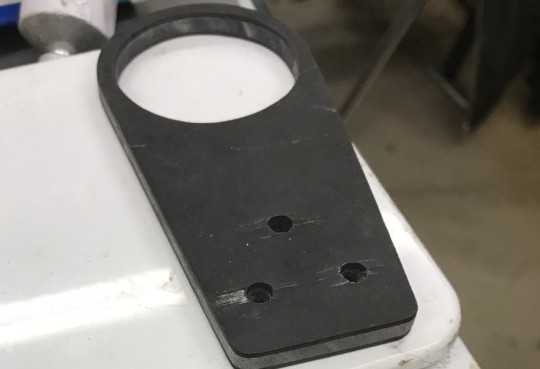
マイクログラスがあれば気をつけていれば、大丈夫でした。
マイクログラスはのり無しを使ってます。
単板焼くときはのりがなくてもくっつきます。
使ってるの▼
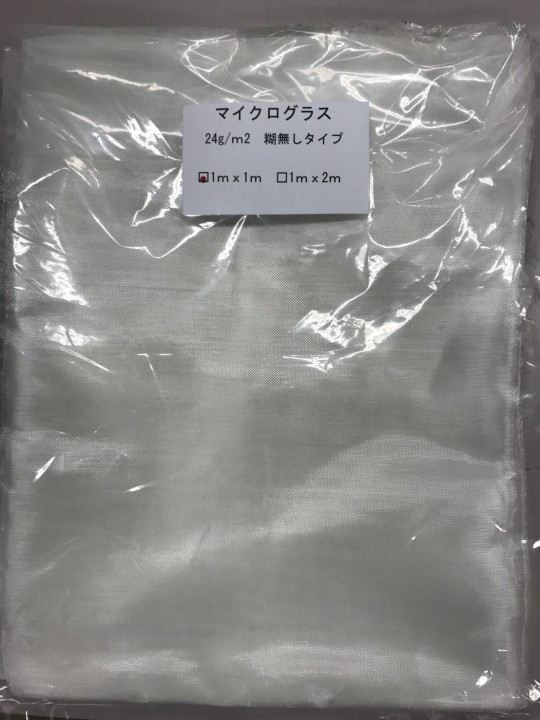
4.真空引きをする。
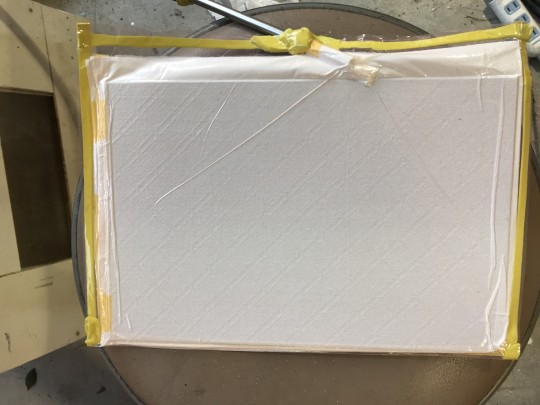
バックフィルムとシーラントテープを使って真空引きします。
最初のころ▼
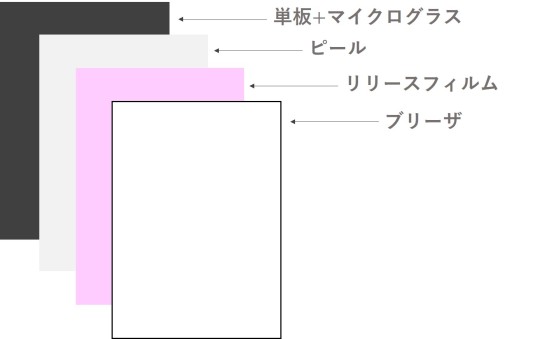
ピール、リリースフィルム、ブリーザの三種類を巻いてました。が
結局▼
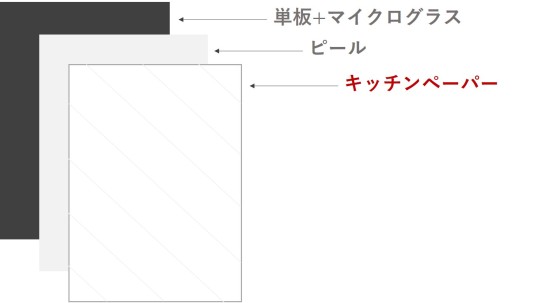
リリースとブリーザは使わずにキッチンペーパーでいいと知り、試してみましたが、何の問題もありませんでした。
コストダウンですね。
補足:ピール
ピールは余分な樹脂を吸ってくれます。
左:ピール有り 右:ピール無し▼

これは、2層の単板ですが、ピール無しだと樹脂だまりができてすっごい表面ザラザラです。見た目のまんまって感じです。
接着するにはやっぱりピールあった方が良いですね。
重量は面積小さいせいかほとんど変わらなかったです。
5.焼く
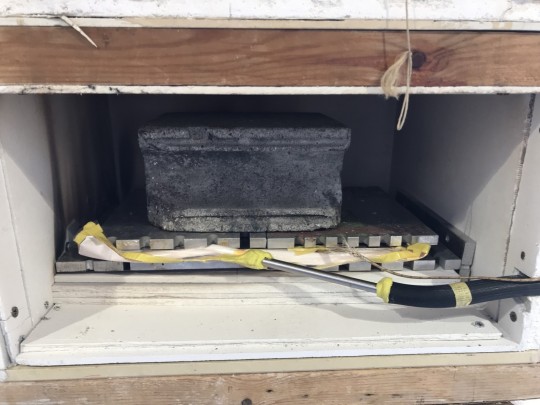
一番下は金属ブロック群です。ゆったり均一にあったまる用です(?)
真空引きしていますが、単板が沿ってしまったら困るます 。
上下をアルミ・ステンレスのプレートではさんで置き、その上に重りを乗せました。
温度はどうしていたかというと、
最初は90度を30分キープして、130度を60分キープの二段階で行っていました。
プリプレグ販売会社とか、論文とかだと結構130度のキープだけとか多いです。
カーボンパイプを作成している会社では、やっぱり2段階の方が良いと言っています。
確かに、パイプなんかはマンドレル等使っていますし、均等に徐々に温度を上げるのが難しいので、キープいるかと思いますが、単板程度の小さいものであれば130度のキープだけでも十分だと思います。
本当は強度への影響も調べたかったですが、時間がなかったです。
炉は、リサイクルショップのオーブンを買って、中のヒーター部分系を回収して、単板が焼けるように製作し直しました。
単盤焼き2号機も有ります。が割愛
(自己責任でお願いします。)
見た目▼
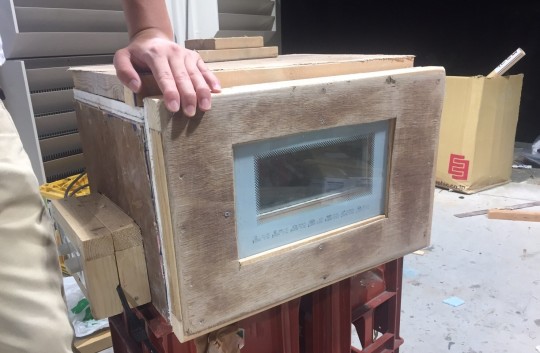
突貫工事なので、汚いです。
どうしてもガラスの窓が欲しかったので、すごく時間がかかりました。
試し焼きの肉▼
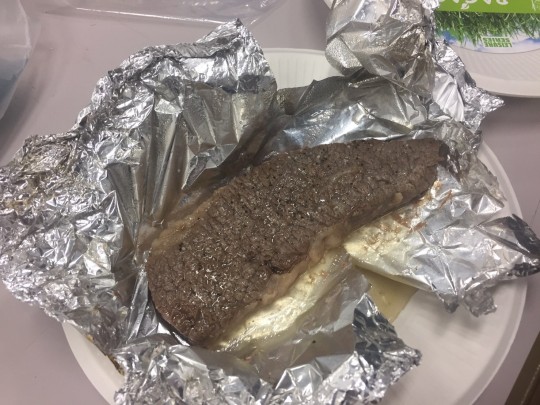
おいしかったです。
6.完成した板

こんな感じでたくさん焼きました。
だいぶ、作業工程も軌道に乗ったのでそこまでしんどくはなかったです。
18年度の実機に使ったのは3枚でした。
結局実験含めて何枚焼いたのかは、見ないふりをしておきます。